Machine Vision Connectivity
Pleora’s machine vision expertise helps systems integrators, manufacturers and camera designers add real-time connectivity to imaging solutions and applications
- External Frame Grabbers – Connect any imaging device to processors and displays over Ethernet and USB 3.0
- Embedded Video Interfaces – Speed design of Vision Standard compliant devices, including cameras, embedded platforms, and X-ray FPDs
- eBUS Software – Simplify application development with end-to-end transmit and receive data delivery for vision, IIoT, and Industry 4.0 systems
Real-Time Connectivity for Cameras, Sensors, Processing, and Display
Use our external frame grabbers to add GigE Vision and USB3 Vision connectivity to legacy camera-based systems and applications
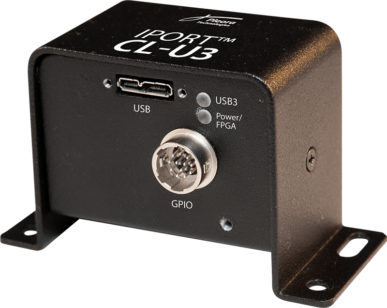
- Stream real-time, low-latency video from cameras and sensors over Ethernet and USB 3.0 directly to existing ports on processors and displays
- Leverage long-distance, flexible cabling and multicasting
- Seamless integration – streaming and control functions of native camera interfaces are maintained throughout the system
External Frame Grabbers
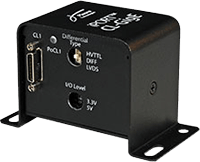
iPORT CL-GigE
Transmit video from Camera Link Base cameras over GigE across a wide operating temperature range
Learn More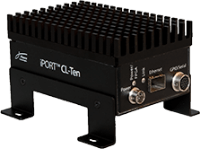
iPORT CL-Ten
High-performance GigE Vision 2.0 connectivity for Camera Link Full and Medium cameras over 10 GigE links
Learn More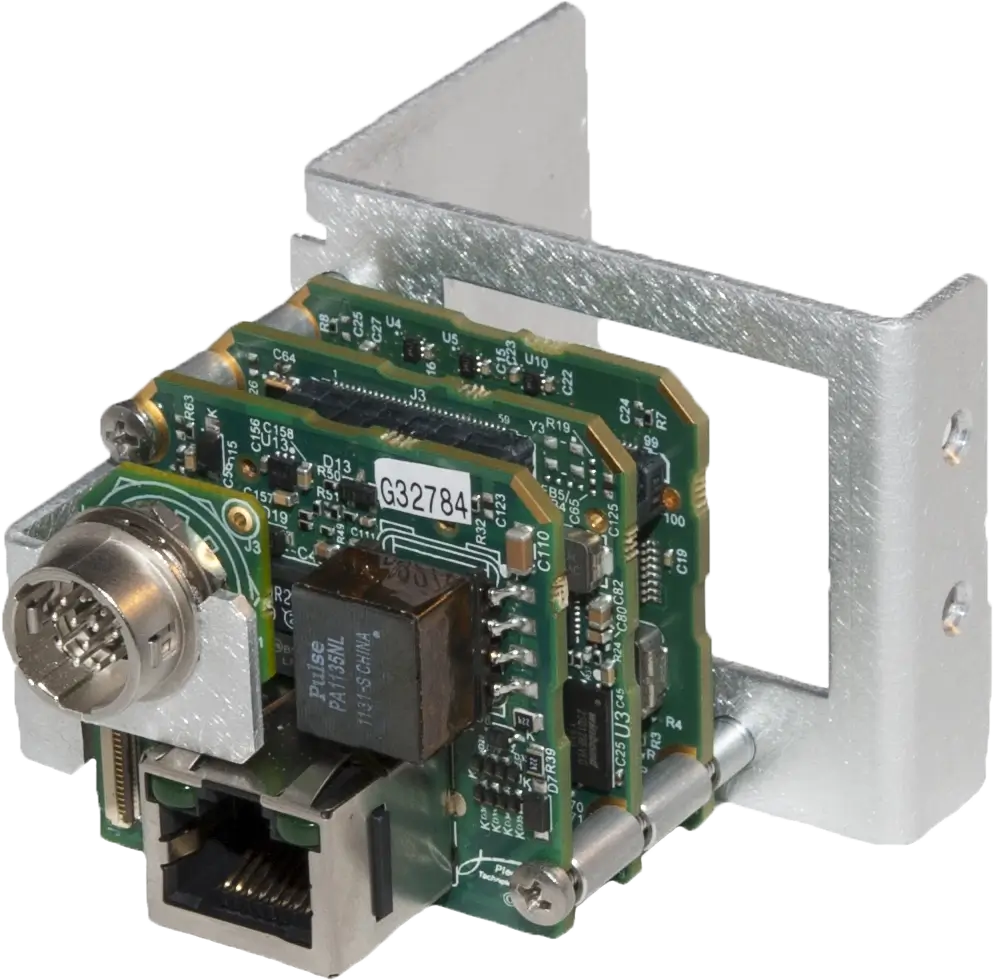
iPORT™ SKB-GigE External Frame Grabber
Enhance the usability of Skoopia® 21Z30S block cameras allowing designers to incorporate them as native GigE Vision® cameras.
Learn More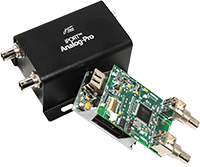
iPORT Analog-Pro
Preserve investments in existing cameras and optics, while converting to fully digital video connectivity
Learn More
RuggedCONNECT™ Smart Video Switcher
Highly integrated standalone device acquires, processes, and displays real-time video sensor data for vehicle-based local situational awareness applications
Learn MoreExternal Frame Grabber Applications
Vision Standards Connectivity for Imaging Devices
Use our embedded interfaces to add highly reliable GigE Vision and USB3 Vision connectivity to imaging devices, including cameras and X-ray flat panel detectors (FPDs)
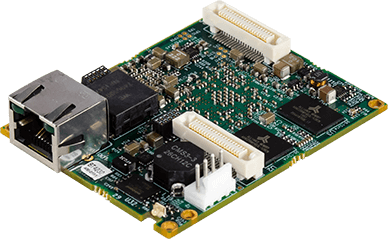
- Stream low-latency video over GigE Vision and USB3 Vision to processors and displays with throughputs from 1-10 Gb/s
- Compact and low power, easily embedded in small-body cameras, flat panel X-ray detectors, and imaging systems
- Designed into industrial, medical, and security & defense applications
Embedded Interfaces
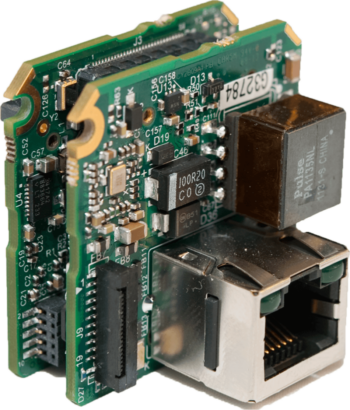
iPORT NTx-GigE
Rapidly add high-performance GigE Vision 2.0 connectivity to systems and cameras
Learn More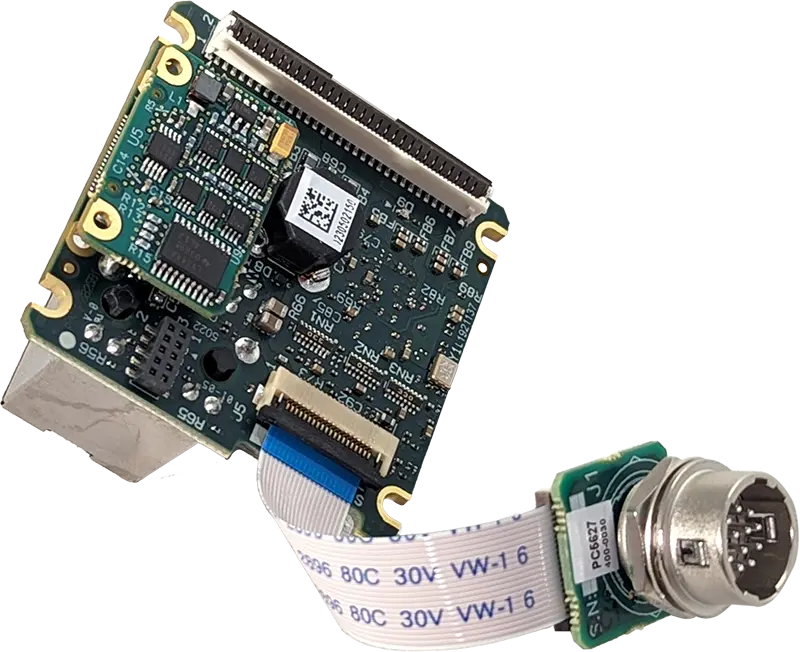
iPORT NTx-Mini-LC Embedded Video Interface with RapidPIX™
Seamlessly increase bandwidth throughput by up to 50 percent while leveraging existing Ethernet network infrastructure
Learn More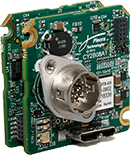
iPORT NTx-U3
Rapidly add high-performance USB3 Vision connectivity to systems and cameras
Learn More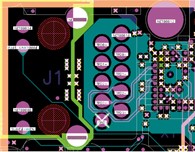
CoreGEV-Tx10 GigE Vision FPGA IP Core
Transmit uncompressed images over GigE Vision at up to 10 Gbps
Learn MoreEmbedded Interface Applications
eBUS Connectivity and Development Software
eBUS streamlines end-to-end data delivery and application development for mission-critical automation, security & defense, and medical systems
- eBUS SDK for image capture, display, and transmission through a simple API portable across Mac, Windows, and Linux
- eBUS Edge software transmitter converts cameras, sensors, and embedded platforms into fully compliant GigE Vision & GenICam devices
eBUS Software
eBUS Training
Our training programs provide an in-depth introduction to eBUS SDK and Advanced Developer for eBUS SDK courses
Learn More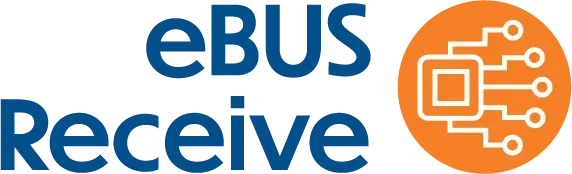
eBUS Receive
GigE Vision and USB3 Vision compliant software that removes watermark from images received
Learn MoreeBUS Training
Our training programs provide an in-depth introduction to eBUS SDK and Advanced Developer for eBUS SDK courses
Learn More