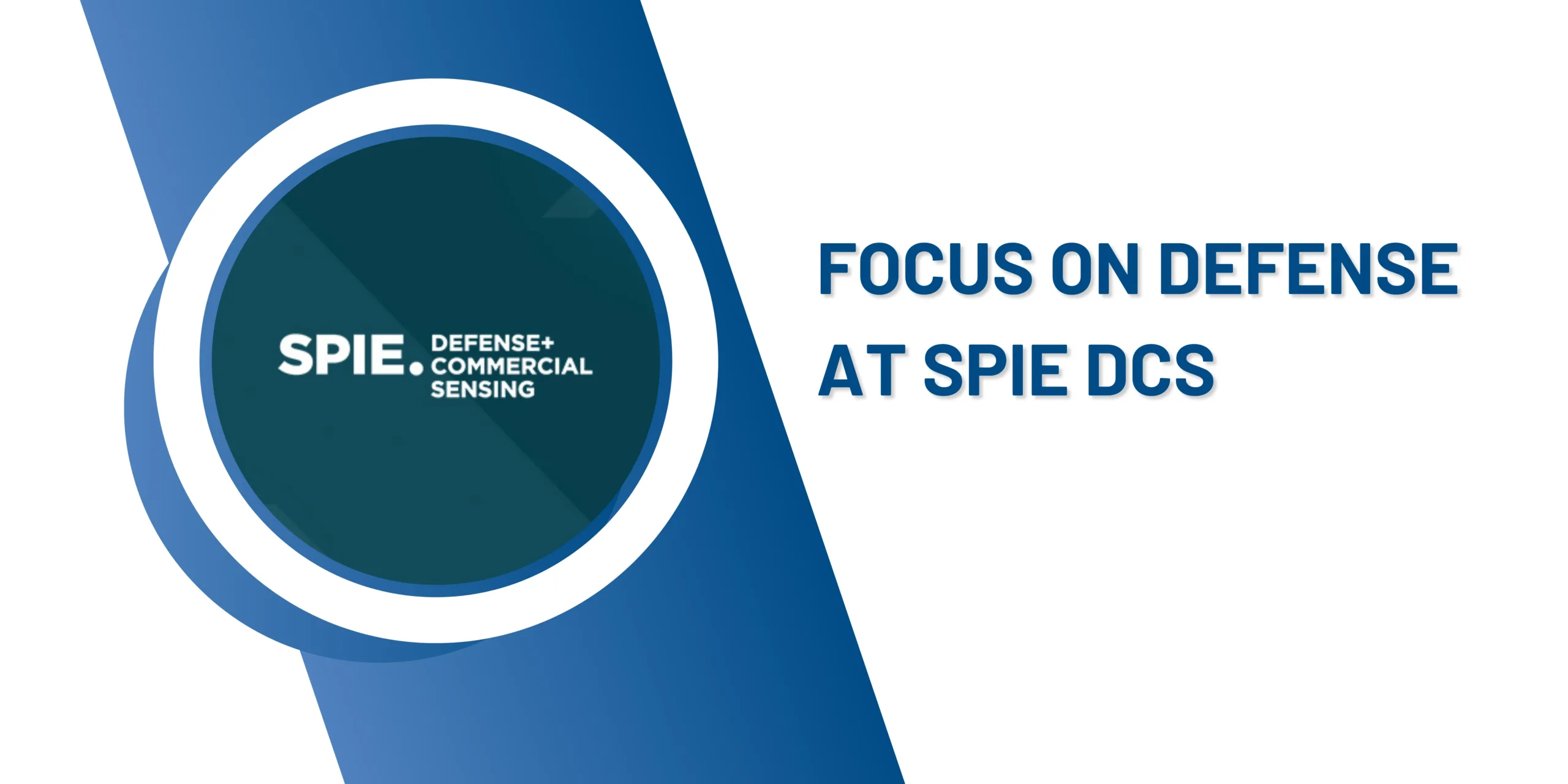
Focus on Defense at SPIE DCS
Insight into vision applications and emerging technologies
Insight into vision applications and emerging technologies
Cautious market optimism and emerging sensor applications in automotive, medical, and logistics sectors
A Series, Pt 9
A Series, Pt 8
A Series, Pt 7
A Series, Pt 6
A Series, Pt 5
Increasing bandwidths pose key processing challenges